 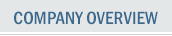 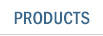 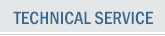 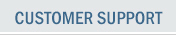 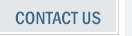 |
|
 |
 |
The Plenco
Difference | What Are Plenco Phenolic
Resins? | Characteristics |
Applications
The Plenco Difference
Phenolic thermosetting resin products are some of
the most adaptive materials in the marketplace and
hundreds of industries benefit from their use. Five
generations of product designers worldwide have
come to rely on phenolic-resin-based materials many
times a day. Plastics Engineering Company is proud
of our history designing materials that have passed
the test of time, whether used in the morning coffee
maker, the Apollo lunar module, or the newest automotive
safety systems.
The market demands custom product development as
resin applications become more specialized. The
type of phenolic resin, its molecular weight, monomer
and moisture content, viscosity or molten flow,
pH, particle size, reactivity during cure, and cure
vapor emission level are but some properties that
determine our products' suitability for a customer.
The Plenco phenolic resin team's mission is to develop,
manufacture, and service useful products that provide
clear value for our customers. Plastics Engineering
Company's experience and ability to select product
formulation options and to use a variety of manufacturing
methods allow tailoring Plenco resins to meet the
requirements and expectations of our customers.
We welcome the opportunity to customize a phenolic
resin product for your application.
Plastics Engineering Company supplies modified and
un-modified novolac and resol phenolic resin products
as pastilles, powders, flakes, lumps, and solvent-
or water-based liquids. In general, customers use
Plenco products to create impervious bonding matrices
with fillers and substrates, to form protective
coatings, to create rigid foams, as a source of
amorphous carbon, or as chemically reactive additives.
top
What are Plenco Phenolic
Resins?
Resins are polymers made by repeatedly linking discrete
molecules (monomers) together to form chains or
networks. Plenco phenolic resins are oligomers (polymers
with a few repeating units) synthesized by repeatedly
linking phenolic (hydroxy-aromatic) monomers with
aldehyde chemicals. The majority of Plenco products
are combinations of phenol (hydroxybenzene, C6H6O)
and formaldehyde (methanal, CH2O), though specialized
applications may require use of substituted phenols
(e.g., cresols, resorcinol, cashew nutshell liquid
distillate), or other aldehydes (e.g., furfural).
Phenolic resin manufacturers polymerize phenol by
substituting formaldehyde on the phenol's aromatic
ring via a condensation reaction. The selection
of suitable reaction parameter results in optimum
molecular weight distribution and residual monomer
content necessary for maximum efficiency when used
by the customer. The wide range of reaction conditions
and monomers available to the resin producer allows
for the production of a variety of resins specifically
designed for use in individual applications.
We present the general chemistry of the polymerization
of phenol with formaldehyde, the most common molecules
used, to provide a general background of resin manufacture.
In aqueous solution, formaldehyde exists in equilibrium
with methylene glycol.
Depending on the pH of the catalyst, these monomers
react to form one of two general resin types: NOVOLAC
RESINS and RESOL RESINS.
Novolac Resins
An acidic catalyst and a molar excess of phenol
to formaldehyde are conditions used to make novolac
resins. The following simplified chemistry illustrates
the wide range of polymers possible. The initial
reaction is between methylene glycol and phenol.
The reaction continues with additional phenol, and
splitting off of water.
The reaction creates a methylene bridge at either
the ortho position or the para position of the phenolic
aromatic rings. The "rule of thumb" is
that the para position is approximately twice as
reactive as the ortho position, but there are twice
as many ortho sites (two per phenol molecule) so
the fractions of ortho-ortho, para-para and ortho-para
bridges are approximately equal.
Branching occurs because reaction can occur at any
of three sites on each ring. As the reaction continues,
the random orientations and branching quickly result
in an extremely complex mixture of polymers of different
sizes and structures. The reaction stops when the
formaldehyde reactant is exhausted, often leaving
up to 10% of un-reacted phenol. Distillation of
the molten resin during manufacturing removes the
excess phenol and water.
The final novolac resin is unable to react further
without the addition of a cross-linking agent. Plenco
novolac resins come with and without a curing agent.
The resins having the curing agent incorporated
cure or "thermoset" to the desired degree
when processed by the customer.
Because an additional agent is required to complete
the resin's cure, the industry commonly refers to
novolac resins as "two-stage" or "two-step"
products. The most common phenolic resin cross-linking
agent is hexamethylenetetramine, also known as hexa,
hexamine, or HMTA. Ground and blended with the resin,
hexa serves as a convenient source of formaldehyde
when heated to molding and curing temperatures.
A special attribute of hexa is that it reacts directly
with resin and phenol without producing appreciable
amounts of free formaldehyde. Hexa cures the resin
by further linking and polymerizing the molecules
to an infusible state. Due to the bond angles and
multiple reaction sites involved in the reaction
chemistry, the resulting polymer is not a long straight
chain but rather a complex three-dimensional polymer
network of extreme molecular weight. This tightly
cured bonding network of aromatic phenolics accounts
for the cured materials' hardness, and heat and
solvent resistant properties.
Certain catalysts can affect the orientations of
the methylene linkages. Catalysts that preferably
promote ortho-ortho linkages tend to preserve the
more reactive para positions:
Novolac resins made with these catalysts tend to
cure more rapidly than the standard randomly linked
resins. Novolac resins are amorphous (not crystalline)
thermoplastics. As they are most typically used,
they are solid at room temperature and will soften
and flow between 150° and 220°F (65°C
- 105°C). The number average molecular weight
(Mn) of a standard phenol novolac resin is between
250 and 900. As the molecular weight of phenol is
94 grams per mole, a Mn of 500 corresponds to a
resin where the average polymer size in the entire
distribution of polymers is five linked phenol rings.
Novolac resins are soluble in many polar organic
solvents (e.g., alcohols, acetone), but not in water.
top
Resol Resins
A basic (alkaline) catalyst and, usually but not
necessarily, a molar excess of formaldehyde is used
to make resol resins. The following two stages describe
a simplified view of the reaction: First, phenol
reacts with methylene glycol to form methylol phenol:
Methylol phenol can react with itself to form a
longer chain methylol phenolic:
or form dibenzyl ether:
or react with phenol to form a methylene bridge.
The most important point in resol resin chemistry
is that, when an excess of formaldehyde is used,
a sufficient number of methylol and dibenzyl ether
groups remain reactive to complete the polymerization
and cure the resin without incorporation of a cure
agent such as hexa. For this reason, the industry
commonly refers to resol resins as "single-stage"
or "one-step" type products. Resol resin
manufacture includes polymerizing to the desired
extent, distilling off excess water and quenching
or tempering the polymerization reaction by rapid
cooling. Because resol resins continue the polymerization
reaction at even ambient temperatures, albeit at
much slower rates than during manufacturing, they
demonstrate limited shelf lives dependent on the
resin character, storage conditions and application.
By manipulating the phenolic to aldehyde monomer
ratio, pH, catalyst type, reaction temperature,
reaction time, and amount of distillation, a variety
of resin structures demonstrating a wide range of
properties are possible. The typical number average
molecular weight (Mn) of a straight phenol resol
resin is between 200 and 450. Plastics Engineering
Company supplies resol resins as liquids or in solvents
with viscosities from 50 to 50,000 cps, or as solids
in the form of lumps, granules, or fine powders.
Organic solvents and the amount of water or phenol
monomer left in the resin control the viscosity
of the liquid resin products. Resol resins are usually
water-soluble to a certain degree.
top
Characteristics
Bonding Strength
The primary use of phenolic resin is as a bonding
agent. Phenolic resin effortlessly penetrates and
adheres to the structure of many organic and inorganic
fillers and reinforcements, which makes it an ideal
candidate for various end uses. A brief thermal
exposure to complete the cross-linking or "thermoset"
process results in attainment of final properties.
The unique ability of phenolic resin to "wet
out" and to cross-link throughout the fillers
and reinforcements provides the means to engineer
the desired mechanical, thermal, and chemically
resistant properties.
Applications benefiting from the hardness, and heat
and chemical resistance properties afforded phenolic
resins include abrasive grinding wheels, friction
linings, refractory products, and other molded parts
used in high temperature or aggressive environments.
For years, phenolic resin's exceptional compatibility
with cellulose fillers has been used to great benefit
for particleboard, plywood, hardboard, oriented
strand board, substrates for melamine laminates
and decking applications. Composites for demanding
applications such as on oil platforms, missile components,
and heat shields are produced using phenolic resins
along with process technologies such as resin transfer
molding (RTM), pultrusion, or filament winding.
Liquid phenolic resins penetrate and saturate paper
and other substrates to provide good mechanical
strength, electrical properties, or filtration capabilities.
Typical examples of these applications include NEMA
electrical laminates, decorative laminates, clutch
and transmission papers, and filtration products.
High Temperature Performance
A key characteristic of thermoset phenolic resin
is its ability to withstand high temperature under
mechanical load with minimal deformation or creep.
In other words, cured phenolic resin provides the
rigidity necessary to maintain structural integrity
and dimensional stability even under severe conditions.
For this reason, phenolic resin binders meet the
challenges of high temperature environments in demanding
applications such as refractory, friction, foundry
and aerospace products. Examples of applications
that take special advantage of the dimensional stability
of phenolic molding compounds are natural gas valves,
automotive brake pistons, pulleys, and hydraulic
and water pump housings and seals.
Chemical Resistance
Phenolic resins accommodate the harsh exposure of
severe chemical environments. The inherent nature
of phenolic resin provides an impervious shield
to protect a variety of substrates from the corrosive
effects of chemicals. Laboratory tests confirm minimal
degradation from many chemicals after prolonged
exposure, often at elevated temperatures. Typical
exposures include gasoline, alcohol, oil, glycol,
brake fluid, various hydrocarbons, and also weak
acids and bases. Protective linings inside tankers
used for bulk transfer of acids and other corrosive
chemical products are often composed of phenolic
resins.
Low Smoke and Toxicity
Burning phenolic resin typically generates hydrogen,
hydrocarbons, water vapor, and carbon dioxide. Phenolic
resin produces a relatively low amount of smoke
at a relatively low level of toxicity. Manufacturers
use phenolic resins extensively to address the safety
concerns of the transportation industry. Automotive
and mass transit industries choose phenolic resin
for its high heat resistance and excellent flame,
smoke, and toxicity properties. Another critical
application is in air support systems for the mining
industry and related electrical conduit supports.
Phenolic resins designed to meet specific flammability
ratings are available. Selective use of inorganic
fillers and reinforcements often enhances protection
in the event of contact with an ignition source.
High Carbon and Char Yield
Phenolic resins demonstrate higher char yields than
other plastic materials when exposed to temperatures
above their point of decomposition. In an inert
atmosphere at high temperatures (600° - 2,000°F,
300 - 1,000°C), phenolic resin will convert
to a structural carbon known as vitreous carbon.
In many ways, this material behaves similar to ceramic
and may actually contribute to structural integrity
when exposed to fire situations. Manufacturers of
structural composite gratings and pipes for offshore
oilrigs, where fires are a constant threat, utilize
phenolic resins for the characteristic. Phenolic
resin is also useful in designing vitreous carbon
articles such as special analytical electrodes,
crucibles for melting rare earth metals, rocket
nozzles, extremely high temperature bearings and
seals, and heat shields for missiles. Automotive
applications that benefit from the formation of
a thin carbonized layer, such as brake blocks and
pads, brake linings, and clutch facings also use
phenolic resins.
The aerospace, defense, and electrical industries
are heavily reliant on phenolic resins. Phenolic
resin advantages include high heat resistance, excellent
dimensional stability, as well as having a United
Laboratories rating. Phenolic molding compound applications
within these industries include electrical commutators,
switches, business equipment, and wiring devices.
Phenolic resin retains its strength at high temperatures,
resists creep under load, and possesses chemical
and corrosive resistance. Phenolic resins are widely
incorporated in household appliances because of
their excellent electrical resistance, dimensional
and thermal stability, and resistance to water and
solvents.
top
Applications
Ablation
Phenolic resin chars when heated to temperatures
greater than 480°F (250°C). This process
continues at very high temperatures greater than
1,000°F (>500°C), until the resin completely
converts to amorphous carbon. This characteristic
contributes to the unique ablative properties of
phenolic resins. An ablative surface is a heat shield
designed to wear away in a controlled fashion at
very high temperatures. Examples are rocket nozzles,
rocket blast shields, and atmospheric reentry shields.
Several aerospace ablative applications specify
Plenco resins.
Abrasives
The variety of abrasive products available in the
market is practically endless, as they have to meet
the specific needs of the individual grinding applications
and substrates. Applications range from simple cut
off wheels to precision sanding tasks, and involve
materials like metal, wood, minerals, and composites.
Generally, there are three groups of abrasive products:
bonded, coated, and non-woven.
Bonded abrasives:
Bonded abrasives like grinding wheels are comprised
of abrasive particles embedded in a bonding matrix.
While the grit used may be from a wide variety of
minerals and abrasive particles, phenolic resin
is the matrix binder of choice. Achieving the optimal
combination of resistance to burst or fracture strength,
flexibility and porosity, coupled to the manufacturing
method, requires optimization of the binding resin
to the specific application of the wheel in question.
Modification of the blend of phenolic novolac powder,
hexa, and liquid resol resin is usually needed to
achieve such optimization. For increased strength,
fiberglass reinforcement inlays are used. These
inlays are themselves typically saturated with a
special liquid phenolic resin.
Plastics Engineering Company tailors powdered and
liquid resins for bonded abrasives to the specific
needs of the customers and their unique cold forming
or hot molding process. Accelerated cure resins
are available as well as dust reduced powdered novolac-hexa
products. Plenco resins are available as solvent-based
flexible phenolic resins for use in fiberglass reinforcement
inlays as well.
Coated Abrasives:
Coated abrasives are flexible grinding materials
typically available as sheets, discs or belts. These
applications require abrasive grains fixed to the
surface of a variety of backings, like paper or
fabric, by special liquid phenolic resin binders.
The manufacture of coated abrasives with their unique
properties requires multiple production steps. Plenco
resins in solvent or aqueous liquid solutions meet
the special requirements of this application.
Non-Woven Abrasives:
Household and industrial applications use non-woven
abrasives, also called abrasive pads. The characteristically
green pads used for cleaning the dishes are the
most publicly visible non-woven abrasive. Manufacturers
of non-woven abrasive parts typically employ the
use of liquid phenolic binders. Plenco phenolic
resins provide the excellent wetting properties
and the short drying times needed by abrasive pad
manufacturers to meet the technical requirements
while achieving a high line speed for improved productivity.
Adhesives
Wood bonding applications such as particleboard
or wafer-board have traditionally used phenolic
resin binders. Due to their specific "affinity"
for wood and wood fibers, special liquid phenolic
resins may be required for the specialty wood adhesives
industry typically in combination with a polyvinylacetate
(PVAc) backbone polymer. Plenco liquid phenolic
resol resins with low free phenol and low free formaldehyde
contents are available especially for use in adhesive
applications. Plastics Engineering Company can also
supply low ash content, soluble solid resol resins,
and of course a wide range of novolac resin-hexa
systems.
Carbon
Phenolic resins have an excellent affinity for graphitic
and other forms of carbon. Manufacturers often use
the resin simply as a binder and adhesive for their
carbon materials. At high temperature, phenolic
resins form a char of amorphous carbon. This means
phenolic bonded carbon materials can be heat treated
to yield an all carbon structure. Because of these
unique properties, phenolic resins find application
in the manufacture of electrodes, carbon-carbon
composites, carbon seals, and washers. Phenolic
resins are the binder of choice for manufacturing
the carbon brushes used in electrical motors, starters
and the like. Depending on the manufacturing process,
powdered or liquid solutions of novolac resin-hexa
blends, powdered resol resins, and liquid resol
binding systems provide the desired binding properties.
Several Plenco phenolic resins meet the requirements
demanded by this technically challenging application.
Coatings
Cured phenolic resins demonstrate exceptional chemical
resistance. Railroad cars, storage tanks and heat
transfer equipment are coated using phenolic resins
as part of baked phenolic coating systems. Plenco
straight phenolic resin systems approved for coating
applications are available and the researchers at
Plastics Engineering Company are ready to tailor
a resin system to the requirements of the customer.
Composites
Phenolic resins are the polymer matrix of choice
in composite products especially when meeting high
flame, smoke and toxicity (FST) properties. Phenolic
resins provide for excellent strength at elevated
temperatures in a variety of environments and are
compatible with a multitude of composite fibers
and fillers. Multiple applications benefit by using
phenolic resins in the following composite part
manufacturing processes:
- Resin Transfer Molding
- Pultrusion and Profile Extrusion
- Filament Winding
- Hand Lay-up
Lightweight and high strength honeycomb structured
core materials for aircraft and other aerospace
applications utilize phenolic binding resins, usually
in a dipping-saturating process. The composite manufacturing
processes and components vary significantly from
product to product and process to process so that
customized Plenco phenolic resins are the best answer
for our customers to find the optimum process and
composite performance.
Felt Bonding
Fiber felt manufacturers use phenolic resins with
reclaimed or virgin fibers to produce thermal and
acoustical insulation for the automotive and household
appliance industries. Felt manufacturers achieve
optimum rigidity, sound absorption and acoustical
insulation performance by varying the density of
the felt product. The versatility of the phenolic
resin to affect the part density mirrors the versatility
of substrate fibers used. Phenolic resins provide
exceptional resistance under all environmental conditions.
Specific applications are:
- Functional components used in visible areas
(e.g., package deck)
- Below surface products used for padding and
sound absorption (e.g., hood liner)
- Rigid parts used as substrate for decorative
material
Felt manufacturers achieve specific performance
requirements by judicious use of Plenco powder resins.
Resin formulation provides for good mold release,
improved compatibility with scrim materials, and
accelerated cure speeds for production efficiency.
Environmental considerations continue to grow in
importance. Plenco phenolic resins for felt bonding
applications exhibit low emission and odor levels.
Low dust level versions of Plenco phenolic resins
are available also.
Foam
Special phenolic resins in combination with the
proper cure catalysts, surfactants and blowing agents
produce foam products. Phenolic foam has a unique
set of properties such as excellent fire and heat
resistance and a low smoke and toxicity rating when
burned. Proper surfactants produce closed cell foams
with excellent insulating R-values. Other surfactants
produce open cell foams demonstrating unique water
absorption properties. Typical application fields
are:
- Floral foam (dry and wet foams)
- Orthopedic foam (for making foot print casts)
- Insulating Foams
Plenco phenolic resins are widely accepted by the
foam industry for their superior consistency, crucial
for the challenging production process.
Foundry
Many technologies are available to foundries for
the production of dies for metal castings. Manufacturers
using the shell molding process experience excellent
dimensional accuracy, surface smoothness and high
production rates using phenolic resin coated foundry
sands. The shell molding process involves first
creating mold cavities and cores by shaping sand
coated with phenolic resin over a not metal form.
Removed from the form and assembled, the mold and
cores create the "negative" shape of the
desired metal form. Hot metal is poured into the
resin-sand mold and allowed to cool. Once hard,
the excess resin-sand material is broken away revealing
the metal part. Some recover the broken away sand
for reuse. The careful selection of sand type, resin
characteristics and coating method results in the
desired mold and core properties such as strength,
rigidity, flexibility, surface finish, part release
and applicability to reuse.
Plastics Engineering Company provides phenolic novolac
sand coating resins in pastille form, for consistent
melting and coating, efficient transport, and low
dust. Resin formulations make use of proprietary
accelerants, plasticizers or release agents to achieve
a wide range of properties. These additives together
with a customized phenol level, melt point, and
hexa amount achieve optimal performance for each
foundry's requirements, like a low peel to improve
release from the hot metal former. The Plenco product
range includes resins for core sands, mold sands,
and recyclable sand.
Friction
Phenolic thermoset resin is the choice for composite
friction materials: the pads, blocks, linings, discs
and adhesives used in brake & clutch systems
that create retarding or holding forces with application
against a moving part. The inherently heat resistant
phenolic resin carbonizes and chars at extreme service
temperatures, it does not melt and smear like other
polymer matrices. This property results in restored
friction properties when the material cools and
"recovers" from hard braking. Formulas
for phenolic composite friction materials are combinations
of friction and wear-controlling agents, reinforcing
fibers and inert fillers blended with un-cured phenolic
resin in an amount necessary to bond the other ingredients
in place with sufficient strength and resiliency
when finished. Judicious selection of the types
and amounts of raw materials used allows for the
optimization of performance with cost and consistency.
Formulas for basic friction applications may contain
5 to 10 different ingredients while specialized
material formulas may include a score or two of
raw materials. Only one type of bonding resin is
typically used. The effect of that one binder on
the final composite's properties depends on the
total formulation and manufacturing method however.
That is, no single type of resin product works optimally
with all friction formulas or applications.
The salient step in the manufacture of phenolic
composite friction materials is the molding and
initial curing of the composite under heat and pressure.
This molding step typically involves pressing a
uniform blend of ingredients in a shaped mold preheated
to 280° - 400°F (140° - 200°C) from
one to three tons of pressure per square inch. The
phenolic resin melts and flows during the molding
operation to coat and then secure the other ingredients
when the resin cross-links or "cures"
to an infusible state. The resin's performance during
the hot molding step is most important to assuring
an efficient manufacturing process. Friction material
manufacturers select the type and amount of binder
resin product used as a complement to the envisioned
manufacturing process, its compatibility with other
raw materials, environmental concerns and the expected
service requirements.
To this end, Plastics Engineering Company is uniquely
suited to assist friction material designers with
a number of liquid and solid novolac (2-stage) and
resol (1-stage) phenolic resins demonstrating a
wide variety of flow and cure character combinations.
The resins can be custom formulated with cure accelerating
or performance enhancing additives. Plenco resins
are suitable for all types of brake and clutch uses,
including pads for lawn & garden equipment and
automotive brakes, blocks for on and off road trucks,
and linings for industrial, oil field and marine
friction applications.
Proppants (Frac Sand)
Oil and natural gas producers improve well yields
using hydraulic fracturing fluids containing round
specialty sands coated with phenolic resin. The
industry refers to these sands as proppant or frac
sands. The hydraulic fracturing fluid containing
the proppant sand is pumped into the well effectively
pressurizing the borehole and fracturing the surrounding
rock. The fluid fills the nascent fissures and the
resin-coated sand works as a prop to keep the fissure
from sealing on release of pressure. Round sand
is used to provide a porous medium through which
the oil and gas can easily flow. Proprietary proppant
sands made with Plenco resins continually improve
petroleum yields every day.
Refractory
High carbon yield, wear resistance, and excellent
particle wetting and bonding properties make phenolic
resins ideal for refractory products. There are
two general categories of refractory products: shaped
and unshaped. Hydraulically pressed refractory bricks,
slide gates, shrouds, nozzles, and crucibles are
examples of shaped products. Examples of unshaped
products are tap-hole compounds, tundish liners
and ramming mixes used in steel making. Plastics
Engineering Company provides phenolic refractory
resins as liquids in a variety of solvents, including
water based systems. Manufacturers may also choose
from a wide range of novolac-hexa powder resin products.
Some companies combine phenolic resins with temperature
resistant ceramic fibers in a vacuum forming process
to manufacture riser sleeves, ladles, and hot toppings.
This application typically uses novolac-hexa powder
resins with low emission levels. Non-hexa cured
Plenco resins are available for this application
to reduce ammonia and formaldehyde emissions.
Rubber
Tires and technical rubber goods use straight phenolic
novolac resins as reinforcing agents. Plenco novolac
resin pastilles are the preferred choice for a manufacturer
who compounds the resin into the rubber for superior
mix consistency and reduced dusting when compared
to using powders or resin in flaked form. Special
effort assures consistent pastille size and shape
to meet the requirements of the automated dosing
systems used by the industry. Plenco phenolic novolac
pastille resins are available in a variety of softening
point and emission level versions. Some rubber applications
require phenolic novolac-hexa powder resin products
in combination with the rubber compound. Plastics
Engineering Company provides novolac-hexa with customized
flow and the hexa curing agent level specific to
each application.
Substrate Saturation
Many applications use liquid phenolic resins to
saturate substrates such as paper, fabrics, and
wood. Phenolic resins receive preference because
of their high mechanical strength, outstanding chemical
resistance, and good flame resistant properties.
Typically, solvent-borne resol resins are used,
but depending on the specific products and processes,
aqueous resol resins or resol cured novolac resins
in solvents are preferred. Typical application fields
are:
- Paper laminates (decorative or functional)
- Engineered wood
- Filter paper impregnation (Oil filters, Gasoline
filters, Air filters)
Plastics Engineering Company provides resins for
the full range of technologies used in this application
field and works to customize specific phenolic resins
to the requirements of the individual customer.
top
|
|
|
|
|
|
|